Reducing cost, speeding time to market, and improving overall end-user experience are three main goals that every good product development firm aims to accomplish — and rapid prototyping technologies can help them achieve this.
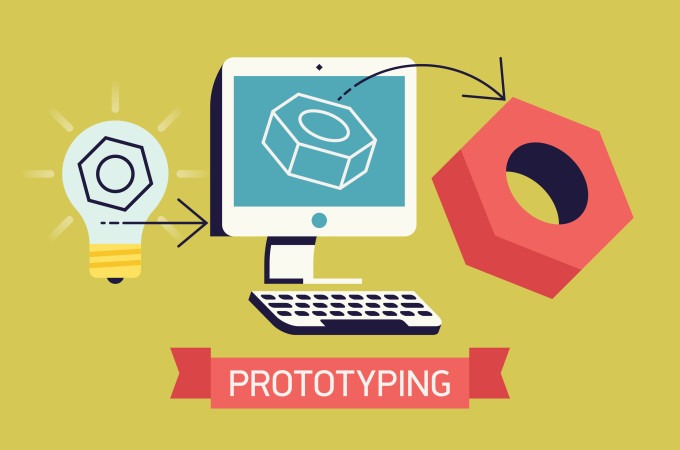
When it comes to product development, there are several steps to the process: concept, design and engineering. Following this, the concept is physically brought to life through the prototyping stage (to test for form, fit and function) prior to entering the final stage of development — manufacturing.
Key to any product development process, however, is fast time to market — and that’s where rapid prototyping comes into play. Specifically, rapid prototyping is defined as a group of technologies that utilize data from a computer-aided design (CAD) file to quickly fabricate a physical product. Compared to conventional prototyping technologies, rapid prototyping creates parts in much quicker timeframes and at cheaper prices, saving companies time and money.
The concept of rapid prototyping came about in the 1980s when the “machine tool crisis” hit, a period where America no longer led the way in machine tools and machine tool manufacturing. As a result, product developers began looking at other methods to create models and prototype parts. Like most technologies in the early stages, there were growing pains with the rapid prototyping initiative. Today, however, rapid prototyping technology has advanced to the point where it isn’t used just for prototyping purposes, but for short-run manufacturing in a variety of industries as well.
Methods/Techniques
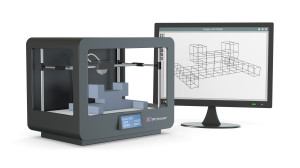
The terms “rapid prototyping” and “additive manufacturing” are synonymous. Unlike subtractive manufacturing methods, which involve cutting away material to create a part, additive manufacturing consists of building the part from the ground up, using only the material necessary. Essentially, additive techniques “grow” the part, and it’s both fast and inexpensive for prototyping compared to alternative methods.
Rapid prototyping largely got its start in the automotive industry as a way for designers and engineers to test ideas as well as parts for form, fit and function in new cars. However, rapid prototyping is used today in just about any product development situation, from automotive to aerospace to consumer products to even the medical industry.
Architects are utilizing the rapid prototyping technology 3D printing to showcase residential and commercial development before it goes to construction — as was the case recently in Detroit, Michigan, where plans move forward to create a downtown district in its Midtown neighborhood, consisting of residential and commercial properties, as well as a new sports stadium. In aerospace, Bell Helicopter used rapid prototyping technologies to develop test parts of wiring conduits for its Osprey chopper. In the automotive field, automakers have taken to 3D printing cars to showcase at various auto shows and other industry events.
The technology is being used to create solar panels, too. It’s even being used in outer space and in educational settings. Rapid prototyping isn’t just for prototyping purposes anymore, and is being used increasingly for short-run manufacturing. A good example of this is in the medical industry, where doctors are turning to 3D printing for making prosthetic limbs and implants.
Rapid prototyping is not lost on hobbyists and entrepreneurs, especially entrepreneurs who are attempting to gain support for a new product idea or innovation. With limited finances available at startup, they’re turning to this more affordable technology to create physical test parts that they can show off — whether via a Kickstarter campaign or some type of crowdfunding site — to gain support.
Benefits/Advantages of Rapid Prototyping
Finance is one of the big drivers of rapid prototyping technology when compared to other types of prototyping technologies: it’s inexpensive. This is largely due to the speed of the process — and as we all know, time equals money.
When it comes to rapid prototyping and 3D printing, the tooling is essentially the CAD file that the equipment is programmed to create. Hence, there’s no expensive upfront tooling costs to pony up and there’s no potentially high re-tooling costs to have to meet if the prototype isn’t up to snuff — just a computer file to adjust accordingly. Therefore, process cycle times aren’t delayed at all.
One of the most popular subtractive prototyping technologies is CNC machining. While tooling isn’t required for this, and CNC machining is viable for some applications, there are several key differentiators between this and rapid prototyping, notably its inability to produce some of the more complex shapes that rapid prototyping technologies can create.
Pros and Cons of 3D Printing
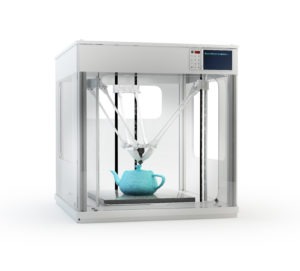
Rapid prototyping consists of additive technologies that quickly fabricate a product. The most common rapid prototyping technology is generally referred to as 3D printing. There are various subcategories of 3D printing — such as SLS (selective laser sintering) and SLA (stereolithography) — but while these techniques differ, they all share the same general benefits. Here is a look at some benefits of 3D printing technology:
No tooling: Because tooling doesn’t need to be created, there are big cost savings.
- Complexity: Parts can be made via 3D printing to be highly accurate and even hollow.
- Fast: Parts can be fabricated in hours, not days. As a result, designers often order or build multiple variations of the prototype part at once to see which model works best in the intended application.
- Flexible: While 3D printing is most synonymous with creating plastic parts, the technology has been adapted to support a variety of other materials as well, such as metals.
- Economies of scale: Additive manufacturing technologies can produce a small number of parts at very reasonable price points. Conversely, when it comes to conventional molding, a mold first needs to be purchased to conduct part runs, which requires more of an upfront investment.
- Easy: While the machines are still fairly expensive, it’s not a complicated piece of equipment to learn.
No technology is perfect, and 3D printing has some drawbacks. Here is a look at some of the technology’s shortcomings:
- Maturity: It’s not as mature as subtractive technologies, such as CNC machining.
- Size limitations: Presently, the parts fabricated via 3D printing are limited by the size of the 3D printer. Most of these machines are small and have limited build chambers for fabricating parts. Larger parts and products have been made using 3D printing, but the technology to date is mostly associated with creating smaller parts and components.
- Materials: Arguably, materials are the biggest disadvantage to additive manufacturing technology. For instance, most materials are not production grade, but rather a similar version of the real thing. This limits some of their functional testing when compared to CNC machining, for instance, which can be used for functional testing and works with hundreds of materials.
SLA vs. SLS
As previously mentioned, two main sub categories of 3D printing involve SLA rapid prototyping and SLS rapid prototyping. SLA is an additive technology that uses a UV laser to cure resin, thereby building parts layer by layer. SLS uses a laser to sinter powdered material in creating a fully functional prototype. (Two subcategories of SLS are DMLS (direct metal laser sintering) and SLM (selective laser melting).
While SLS and SLA each are able to fabricate a prototype, they differ in their 3D rapid prototyping methods. For instance:
SLA parts are generally cheaper to build based on the process.
SLS is able to fabricate parts in a nylon material, which is tough yet flexible.
SLA parts generally have a smoother surface finish than SLS parts.
SLS parts tend to be more durable than SLA parts.
SLA parts are better for display items, not necessarily to test for function.
Parts created via SLA are generally more accurate.
Rapid Prototyping Services
While rapid prototyping machines have become more compact and more affordable over the years, a good piece of equipment is still expensive. That’s why many product development firms are more apt to outsource prototyping than bring it in-house. By uploading their CAD files to a qualified rapid prototyping service, they’re putting their product in the hands of experts. These experts can help identify any product flaws in the CAD file and then work with product developers to correct it. Furthermore, the turnaround time with rapid prototyping services is usually very fast.
For more information on rapid prototyping services, contact us today.