For startup businesses looking to break into the market with a new product, injection molding can play a major role in getting up and running. This may run counter to what you’ve heard, since the myth persists that plastic injection molding for startups is out of reach due to the smaller size of the business. In actuality, choosing the right plastic injection molding partner can give you access to the same processes and capabilities that higher-volume and more established businesses use, streamlining and speeding your time to market.
Principles of Plastic Injection Molding
If you’re unfamiliar with plastic injection molding for new business, let’s first cover what the process entails. In plastic injection molding, a base plastic material (typically called a “resin”) is heated and liquefied, then injected with pressure into a die containing multiple cavities in the shape of the product or part to be formed. The die is usually made of metal, but can be created from other materials, as well. After the resin cools to a solid form, the die opens and the pieces are ejected from the cavities.
The steps in the process are:
- Design: From initial concept, the design can then be tailored for the best compatibility with the injection molding process.
- Die manufacture: Typically the most time-intensive portion of the process. A die is manufactured in two halves (so that it can open and clamp shut), and — in addition to cavities in the shape of the piece to be produced — contains channels for the molten plastic material to flow through to reach the cavities.
- Production: The process described above, where the liquefied plastic is injected into the die, cooled and pieces are ejected.
- Finishing: If any aesthetic finishing processes are needed, they occur at this point. Excess material, known as “flash,” is also trimmed from any parts where it occurs.
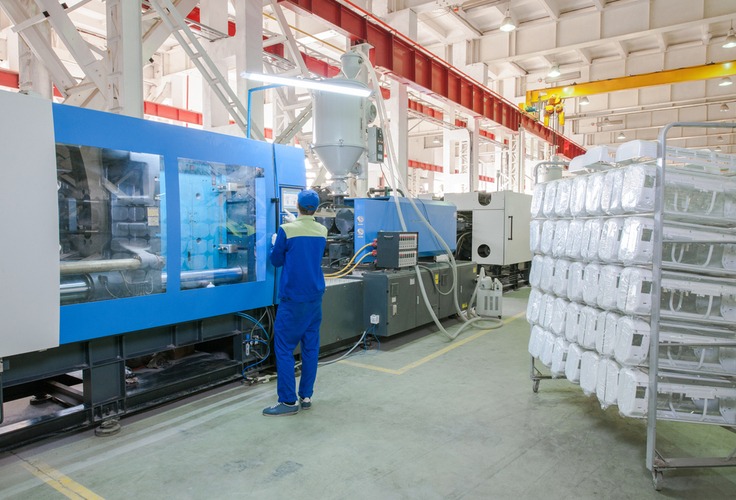
Production Challenges for Startups
For startups, there are several production obstacles to overcome as you get established:
- Cost: Cost is the No. 1 challenge and barrier for turning an idea into a reality. Upfront investments for manufacturing equipment are often too high to consider for businesses that are just starting, so it’s necessary to work with a manufacturing partner. For new companies, however, the next issue also presents a challenge.
- Production minimums: Most injection molding service providers require relatively high order minimums to take on a job. However, when orders are just beginning to ramp up for a smaller business, the risk in committing to high-volume production is often simply too great to consider. Thus, production minimums for many plastic injection molders are out of range for startups.
- Access: Depending on your location, injection molding services for startups can be difficult to locate or may not offer the capacity to take on your project, instead prioritizing higher-volume orders.
- Information: Manufacturing processes can seem complex to the entrepreneur or layperson, creating an information gap that complicates the service partner sourcing process. It is our hope that this article provides a simple overview of the injection molding process and enables you to make a more informed decision.
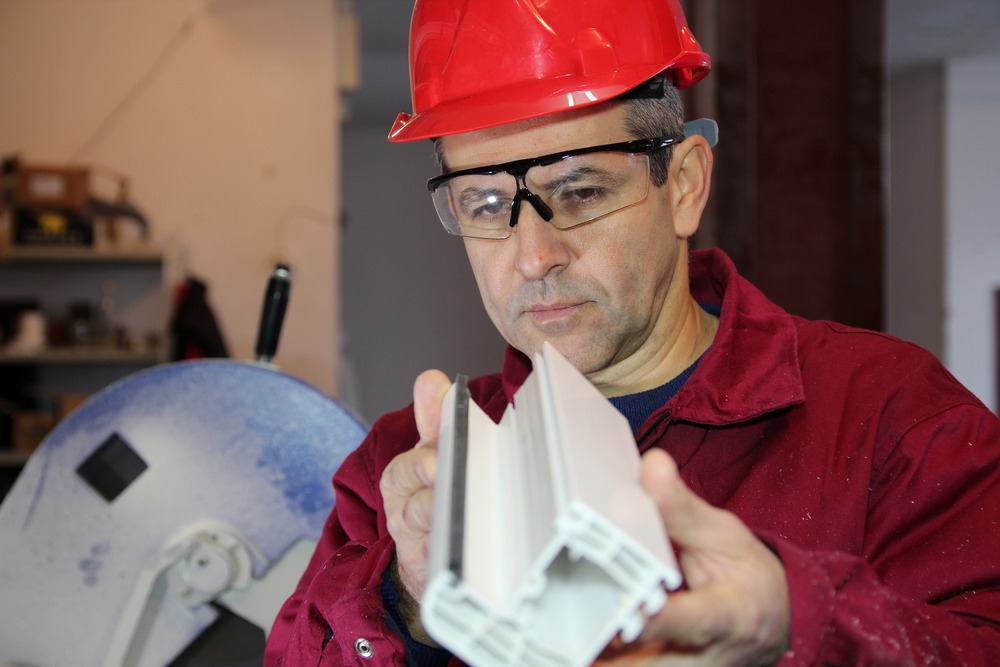
Finding Plastic Injection Molding Providers for Startups
Fortunately, there are injection molders out there for new businesses and startups. Below, we’ll explain how to locate them and why it’s worth your time to do so:
- Seek a provider that specializes in low- and medium-volume jobs: While many molding service providers will state that they take any job, in reality, they will prioritize a higher-volume order over a lower-volume one if capacity is an issue. Choose a provider that specializes in helping businesses like yours get up and running. It will have the experience to help you get the project right, and you don’t have to worry about delays due to larger orders.
- Investigate alternative mold materials: High-volume injection molds are usually made of tool steel, which is durable, long-lasting — and expensive. Softer, less-pricey metals can also be used for molds when lower volumes are required. In addition, molds can even be created from materials like sand for single or short-run requirements such as prototypes.
- Look at other methods: 3D-printed prototypes for startups are commonly found and present a viable way for you to generate early-stage prototypes for testing. Keep in mind, however, that creating a prototype made from the same plastic material as your end product will be a valuable step to take prior to production. Even if you use other prototyping methods earlier in the process, an injection-molded prototype can help identify any last-minute manufacturability, design or functionality issues.
- Use a production-quality prototype to your benefit: In addition to the product development advantages of an injection-molded prototype, it can provide an extra boost when seeking funding or pitching your product to distributors and retailers. A functional prototype with the same appearance as the finished product will give these stakeholders the confidence that you mean business and are ready to sell your product. Lower-quality prototypes, contrastingly, require more of a leap of faith to connect with the finished piece.
- Work with a versatile service provider: Injection molding is used so frequently in manufacturing because of its versatility. Find a service provider that is as flexible as the process. For example, there are thousands of resins that are suitable for injection molding, with different characteristics, material properties, appearances and costs. A service provider that is experienced with a wider range of materials will be able to help you select the right material for your product in the most cost-effective way.
At RevPart, we offer prototyping services with a wide range of production capabilities, such as plastic injection molding. We specialize in short- and medium-volume jobs, including prototypes, and have worked with numerous startup companies to help get them access to production-quality prototypes that fit their budget. We draw on our experience with new businesses to provide the best service possible, and we hope that this guide helps you identify the right plastic injection molder for you.