Prototyping is one of the most important steps in the product design and development process, and in many ways, it can be the linchpin of your product cycle. Consider that during the prototyping phase, you are actively bringing your product through from concept to reality — the prototype is what bridges these two bookends. Prototyping is likely when you’ll learn the most about your product, because so many questions will be answered — how does it look and feel in a real 3D form? How easy or difficult was it to produce? Is it structurally sound? Is it feasible to move to production?
The answers to these questions define the actual process of manufacturing your product, which will often end up being different from your initial sketch or CAD drawing. Without adequate, dedicated prototyping, you are essentially flying blind; hoping that your product will turn out the way you envisioned it, rather than knowing for sure.
There are a few important factors to consider when having your prototype created: the process and its results reward research and careful consideration of your options. A major consideration is the material you choose. The different qualities of the various materials available — and how they work with different processes, like injection molding and 3D printing — play a big role in how your prototype turns out, and how, as a result, you make choices about the production process.
Why is prototyping important?
We’ve already talked a bit about the big-picture scenario, but let’s take a quick look at why, practically speaking, a prototype is so critical to the product development cycle:
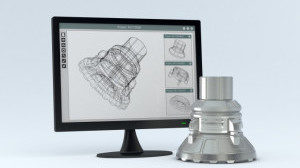
Manufacturability is a key consideration. If you are expecting to manufacture your product through injection molding, you need to know beforehand whether it’s suited to that process. 3D printing can show you what a product looks like, but it won’t let you know how it handles the molding process. Fortunately, there are options for prototype-grade molds for injection molding. These molds are good for runs of several thousand parts, giving you a first-hand look at the injection molding process for your part, without the prohibitive cost of steel or other production molds.
That’s not to say that rapid prototyping and 3D printing don’t have an important place in these preliminary steps. If you simply want to get a feel for how your 2D concept occupies the physical space, rapid prototyping is the right choice. Here, you’ll be able to get a sense of the proportions of your product, its structural strengths and weaknesses, and even its aesthetics — all important factors for optimal end results.
Why is proper material selection important for prototyping?
For a number of reasons, your material selection can affect the qualities of your prototype. Some things to consider are:
- • Fidelity to your original CAD drawing/digital file. Is the material conducive to high accuracy in 3D printing/rapid prototyping?
- • Comparison to your intended production material. If you’re using a different material than your intended production material, will they respond to your process the same way? For instance, will they both fill an injection mold easily? Do they have different cooling times?
- • Suitability for your prototype process of choice. Similar to the above, are you using a material that’s compatible — or even available — for your chosen process? Is your plastic or resin available in spool form for 3D printing, for example?
- • Cost. Are you using the most cost-effective option for a non-production grade piece?
- • Functionality (with factors like material flexibility, hardness, durability, and so on). If desired, will your material be able to mimic the intended functionality of your final product?
- • Aesthetic versatility. Is the material available in various colors, or can color be easily altered by adding powders or other pigmentation?
- • Environmental concerns. Can your prototypes be recycled or otherwise reclaimed?
These are just a few of the questions you might ask yourself when choosing a plastic for prototyping — the list goes on, depending on the product and your concerns. Read on to learn more about available options.
What plastics are available for prototyping?
With so many materials available, this list is an overview of some of the most commonly used plastics in prototyping, and important things to consider when making your choice.
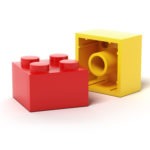
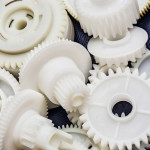
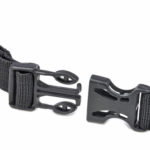
ABS: Think of ABS as the jack-of-all-trades of plastic prototyping. It’s a readily available, easily machinable material that performs well in just about every area you’d be concerned with for a prototype. With a low melting temperature, ABS can very easily be injection molded. It’s also well-suited — and easily found in spooled filament form — for 3D printing. Although, 3D printed ABS parts may lack the functional strength of injection molded parts. ABS can easily be pigmented, and is also highly receptive to finishing like sanding, smoothing or texturing.
However, there are situations where ABS is not the right choice. It’s not suitable for medical or other bio use, so if that’s your industry, you may want to explore other options for prototyping that may be more similar to the production material. Its low melting temperature also means that if your injection molded prototype has varying wall thicknesses, uncooled liquid ABS might be more susceptible to flowing from thicker to thinner areas.
Acetal: If you’re sure you want to go with injection molding for your prototype, Acetal can be a great choice. Harder than most other plastics and with a lower porosity, Acetal has a very low friction. It’s also better suited to higher temperatures than materials like ABS. For functional prototypes requiring low friction, like gears and zipper mechanisms, Acetal works particularly well.
Nylon: In powdered form, nylon can be used in SLS 3D printing for a variety of part types. A key benefit of nylon is its strength throughout a wide range of thicknesses: thin parts or part sections can be created that are flexible while still structurally sound, making nylon a strong choice for electrical connectors and enclosures. Nylon is, however, susceptible to warping, and material costs can run higher than other options (although the SLS process means that some powder can be re-used).
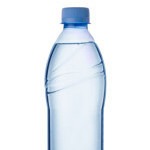
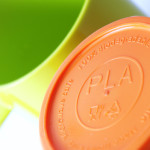
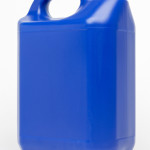
PET: Commonly used for bottles and containers, a major benefit of PET is its shatterproof strength, even in thin constructions, and its light weight. PET melts at a very high temperature and gains a high viscosity at these temperatures, meaning it can more easily completely fill a mold, even for complex parts.
However, these characteristics of PET also mean that it requires a bit more of an involved injection molding process, including hot runners, pre-drying, and rapid cooling. This means more setup, more steps and higher costs associated. PET is best chosen as a prototype material for more specialized constructions (like very thin walls) where its specific qualities are required.
PLA: For rapid prototyping, PLA holds one benefit over all other materials: it is made from renewable resources and is completely biodegradable (while most other plastics discussed here are recyclable, but formulated with petrochemicals). For situations like prototyping where it’s unlikely that the finished product will be required for long-term use (and thus likely to be discarded), PLA is the environmentally conscious choice.
PLA is also suitable for production use in medical devices, meaning that you can 3D print with it and get a prototype that will mimic the qualities of your finished product. One drawback: PLA is a bit more easily breakable than other materials, and so is not as suitable for high-stress or tough-duty functions.
HDPE: High-density polyethylene (HDPE) is easily 3D printable and creates very strong prototypes. A key benefit is that 3D printed HDPE parts can replicate the strength and other qualities of injection molded HDPE, letting you create prototypes that are very similar to production parts, with the same material, at a much lower cost.
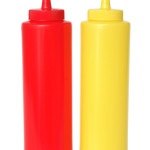
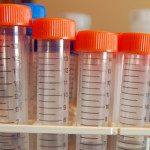
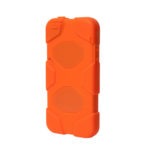
LDPE: Low-density polyethylene (LDPE) is not as strong as HDPE, but its lower density means it is much better suited to parts where flexibility is required. For softer parts that are still able to withstand other welding or machining processes, LDPE is a good choice. It is not, however, able to withstand the toughest duty conditions, under which it may break.
Polypropylene: For injection molded prototypes, polypropylene stands head and shoulders above other options for two specific uses: living hinges and medical devices/components. As a material for those applications, it can be difficult to find another option that recreates its specific qualities, so you will often want to prototype using the same material. The specific strengths of polypropylene are high flexibility, ability to stay intact at very thin gauges (ideal for living hinges), and resistance to bacteria and other contaminants (ideal for medical functions). It also has a very high melting point, making it more receptive to sterilization.
TPU: TPU is a very soft and flexible material used for 3D printing prototypes. It is well-suited for applications where flexibility as well as tensile strength are required of the part, such as hoses, belts, gaskets and similar components. It is a good choice for testing for mechanical functionality of products where these qualities are necessary; however, it does not stand up to the extremely high temperatures that other flexible materials, like polypropylene, can.
How to Choose the Right Plastic for Your Prototype
With all of these options (and more), it can seem like a challenge to make the right choice. It can help to ask yourself a few questions:
- • What stage am I at with my product design? Earlier stages might require less functionality and greater emphasis on design, while you may desire a stronger, more functional material as you move closer to production.
- • What do I want to learn from this prototype? If you simply want to see the dimensions and proportions of your product in 3D space, you don’t necessarily need mechanical functionality. If you’re hoping to test it in use cases or with other components, you need a plastic that can impart functionality, with greater strength and resistance to breaking.
- • What are my cost considerations? It’s not always practical within a budget to choose the highest quality material. Weigh the options of every material against your needs in order to get the most out of your prototypes.
- • What do I need to test for? It’s easy to find out the cracking point or melting point of your options; you don’t necessarily need to create prototypes to execute tests in those areas. Focus more on the specifics of your product.
- • How specialized is my product? Will it require the particular qualities of polypropylene or nylon? Is it important that the prototype reflects those qualities, or is a material like ABS suitable?
Conclusion
In essence, it is up to you to determine where you are in the design process, and where you still need to go. In making that determination, it’s important to be thorough — both in gauging your progress, and in making choices at each step. However, while you are the expert in the area of your product and development process, there are other experts available who can help you as you move it along to a reality — be sure to take advantage.