In manufacturing, there is sometimes a notion that there are “metal applications” and “plastic applications.” In other words, there’s an assumption that these are applications for which one type of material is just more well-suited, and the other type of material can’t be used.
If you haven’t started already, it’s time to rethink those ideas. For anyone in the automotive industry, you likely have at least some familiarity with metal-to-plastic conversion — the practice of changing part and product design to incorporate plastic instead of metal. Did you know, though, that there are numerous other industries where, when the choices are plastic vs. metal, plastic is just as good of a choice?
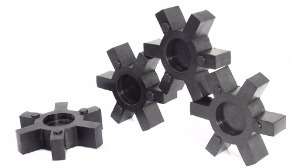
It’s true. The automotive industry is only the beginning of the possibilities of metal-to-plastic conversion. Nearly any transportation-related field can also benefit by investigating the advantages of metal replacement plastics: shipping containers, railroad manufacturing, heavy trucks and RVs, aircraft applications, and more.
Below, we’ll look at the advantages that plastic parts can offer over metal ones, in the right applications.
Plastic is less expensive. In nearly all cases, the raw material for plastic manufacturing is less costly than that for metal production. Depending on the material in use, plastic can also be easier to access than metal — shortages in plastic are essentially non-existent, whereas metal prices often fluctuate according to supply and demand. This fluctuation can drive up your costs in scenarios where waiting out the market isn’t an option.
Plastic weighs less. This simple benefit is one of the top reasons that manufacturers switch from metal to plastic. The benefits of reduced weight make themselves apparent across the board — in manufacturing, shipping and (of course) in the end application of the product.
On the manufacturing side, your sourcing costs are much lower, since lighter plastic material can be shipped that much less expensively. Your shipping costs to customers are lower as well, for the same reason.
The end use is where the weight benefits of plastic become extremely apparent. In transportation, any type of vehicle will see fuel efficiencies from a lower operating weight. In industrial applications, plastic offers maneuverability and handling benefits when compared with metal — think of the large sliding compartment doors in shipping containers. They can provide the same strength and rigidity (more on that below), with a much lower weight, making them considerably easier to move.
Lower weight can also help in meeting regulatory standards for vehicles, such as reduced emissions and increased fuel efficiency. In the automotive industry and beyond, this one benefit has driven untold numbers of decisions to switch from metal to plastic.
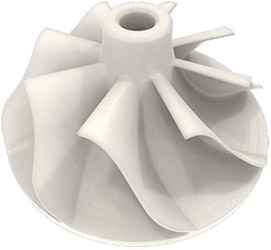
Plastic can offer greater strength. There are a vast number of plastic materials that offer tensile strength comparable to the metals that are typically used in these applications. In numerous cases, that strength and rigidity can even exceed that of the metal previously in use. In many of the transportation applications we’ve discussed here, strength is a key requirement of the material. Countless transportation components are subject to high, repetitive stress, sometimes in extreme environments. Strength and reliability simply cannot be sacrificed in a switch from metal to plastic.
Fortunately, plastics are more than up to this task. It’s difficult to imagine anyone making the switch from metal to plastic if the strength requirement wasn’t met. Yet the combination of lighter weight and comparable strength has made it an easy choice for numerous manufacturers.
Plastic allows more design flexibility. The nature of metal manufacturing means that a limited range of processes can be applied to metal in an efficient manner. More complex features in metal require exponentially more processing — increasing manufacturing times and driving up costs.
Plastic molds, on the other hand, allow for a much broader range of design choices. Complex features can easily be designed into the mold, and the difference in time and cost between producing a simple piece and a complex one is negligible.
Plastic can save time and money on finishing and assembly. The design flexibility offered by plastic means that pieces that would normally have to be constructed from several metal parts, and then welded or otherwise assembled together, can be manufactured in one piece with a plastic mold.
In metal manufacturing, the most efficient way to produce complex features is via assembly, as opposed to in the manufacturing process itself. Any way you look at it, this is a more effort-intensive (and thus more time- and money-intensive) process than single-piece plastic manufacturing.
In addition to reduced assembly costs, plastic components can typically be used right out of the mold, reducing finishing time and cost. Metal parts, on the other hand, may need to be ground, smoothed and otherwise finished in order to be ready for the end application.
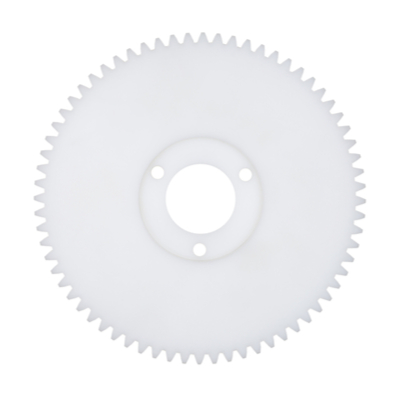
Plastic offers more material choices. Plastic material choices — and the physical properties that accompany them — are nearly endless. Moreover, custom plastic materials can be designed and produced extremely easily, making it an attractive option for applications where specific material properties are required.
Even when considering the number of alloys available, metal material selection is, relatively, much more limited. There’s a greater chance you’ll run into a “dead end” if searching for a metal with physical properties for a unique requirement; whereas those dead ends essentially don’t exist for plastic, for most common applications. Engineered plastic materials are a booming business, meaning you’ll easily be able to source and work with a provider.
Manufacturing costs are lower. Plastic manufacturing processes are, in general, more streamlined and efficient than those for metal — thus, they cost less as well. Whereas metal production is typically done via machining — removing material to shape each piece — plastic injection molding creates numerous pieces at once, with vastly less waste. These efficiencies add up over time to much lower costs for you.
We hope that after reading these advantages, you’ve identified a few ways — or more — that you might benefit from metal-to-plastic conversion in your products. The practice continues to be on the rise, and perhaps it’s time for you to join.