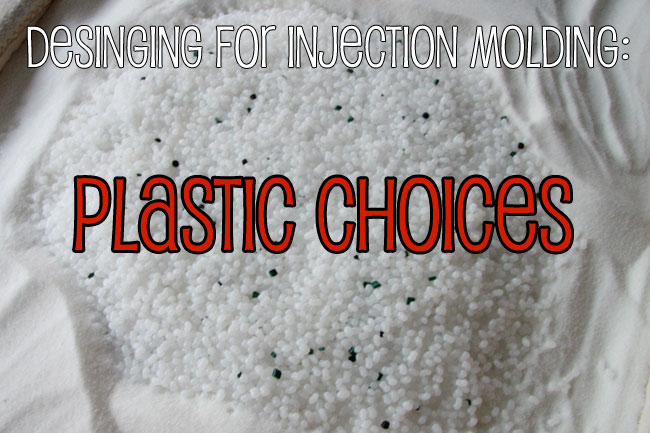
Plastic Choices
Although you might be tempted to think that all plastics are the same, they aren’t. The plastic in my Tupperware is very different than the plastic in my computer mouse. Having your material choice in mind as you begin designing can help guide your decisions during the design process so you won’t have to make extensive changes later.
While it’s possible to design your part first and pick your material later, sometimes you can’t do that. If your design needs something specific—like being super strong or being transparent—it’s best to start with your material in mind so you can understand its peculiarities and work your design around them.
Because each mold is created specifically for the type of plastic that you selected, changing your mind later in the process can be a costly redo. Each type of plastic shrinks a little differently, so if you decide to use a different plastic after the mold is built, it may not be possible. Understanding which type of plastic you want to use at the beginning of the design process can save you time and money later.
A few popular resins are ABS, polycarbonate, and glass-filled nylon:
ABS is an inexpensive, general purpose resin used for handheld electronic devices, the housings of power tools, and many other products. It might scuff or scratch but it isn’t prone to breaking. Although it can have some problems sinking during the cooling process, a well-designed item won’t show serious signs. It’s an opaque plastic but transparent versions are available.
Polycarbonate is a slightly higher end resin that comes at a medium range cost. Because it’s transparent and super strong, it’s often used for bulletproof windows. It does have a tendency towards sinking though—even if the sink doesn’t appear on the surface, there may be voids inside the material that can have serious effects on its strength.
If you want to combine the strength of polycarbonate with the anti-sinking of ABS, you can combine the two resins into one to try and alleviate the problems.
Glass-filled nylon is a very strong plastic that resists many solvents that can damage ABS and polycarbonate. Unfortunately, it’s extremely prone to sinking, so good design is critical. If you’re going to use glass-filled nylon, it’s important to know it at the beginning of the process so that you don’t need to make major alterations to your design right before you want to get a prototype.
Color
An important aspect of the plastic you choose is its aesthetic value. Aside from your surface finish (more on that later), the most obvious detail that potential customers will notice is your product’s color.
Unfortunately, most plastics only come in a narrow range of “natural” shades from clear to dark brown or black.
If those colors aren’t to your liking, some plastics can be spray painted after the parts have been made. This opens up a wide variety of options but adds time to the production.
The most common choice to change the color of your part is to add dye pellets right into the plastic before it’s melted. Some of our competitors cite problems with this method, as adding the wrong amount of dye can cause swirling or marbling in your plastic…but making sure we have the perfect color for your item is up to us, and you will never see color problems like this in your product.
We also have a service that a lot of our competitors don’t: we can match the color of our plastic to any of the colors in the Pantone Matching System. This allows us to exactly match your desired color, no matter what it is (still without errors like marbling).
Don’t want to miss any of the tips in this series? Subscribe to our newsletter to get them delivered straight to your inbox.
Defining Some Terms | Plastic Choices | Size Variatoins