CNC Milling Services
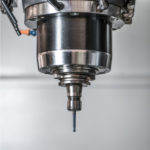
CNC milling is a subtractive manufacturing process that uses different tool types to remove or grind material from a piece of raw stock according to a programmed design, producing the desired part shapes and features. RevPart offers 5-axis CNC milling services, meaning that both the stock and the tools can move during the process, enabling the greatest versatility of design. We also specialize in plastic CNC milling for a broad range of material types.
Typical custom CNC milling applications include manufacturing holes, slots and other recessed structures, as well as dovetail joints, bevels and more. Precision CNC milling is also great for producing threaded features. Additionally, RevPart’s excellent CNC milling services can shape part contours. Our plastic CNC milling services are most often drawn upon by the medical, aerospace, automotive, electronics, industrial, space and consumer industries.
CNC milling services involve mounting a piece of plastic, metal, wood or other material on the bed of a milling machine, where the cutting tool cuts the design out of it. The process begins with the creation of a CAD model in software platforms such as AutoCAD or SOLIDWORKS. The model is loaded into the CNC system, which is what guides the automated cutting tool during the milling process. Once the workpiece is properly set up in the machine, the milling process can begin. The tools rotate to cut away the unwanted material until the finished piece remains.
Benefits of CNC Milling Services
CNC milling offers numerous benefits, which is why it is so broadly used across industries and applications. As a longtime CNC milling parts manufacturer, RevPart is committed to helping you realize these advantages and make a positive impact on your project. Primary CNC milling benefits include:
- Cost efficiency: As one of the most common manufacturing methods in use today, CNC milling is a cost-effective solution to shape plastic parts and features. Material costs are typically low and setup time is minimal. Plus, it is a relatively high-speed technique that does not often require additional finishing processes, meaning less machine time and increased productivity.
- Shape versatility: Custom CNC milling is capable of producing a wide range of shapes, contours and part features. With 5-axis milling, our processes are especially versatile.
- Smooth aesthetics: Create smooth corners, contours and an attractive appearance for consumer products and other applications. Although CNC milling can leave cut patterns on plastic, additional finishing is often not desired or required, keeping costs low and speed high.
- Material versatility: CNC milling services are suitable for any plastic that can be machined, making for a wide range of materials to compete with metal options. Generally, custom CNC milling for parts enables them to cost and weigh less, offering substantial advantages while maintaining similar strength.
CNC Milling Design Considerations and Options
In this section, we will look at some of the design considerations for our milling services.
- Various recessed shapes: CNC milling is often used to create recessed structures, such as holes, slots, snap connectors and more. These recessions can be threaded or unthreaded. In fact, milling is often used to add features to already-machined parts, although the process is perfectly capable of producing entire parts on its own.
- Rounded corners: Note that CNC milling produces visible cut patterns which — if a perfectly smooth finish is required — may require additional processing after milling.
- Rounded corners: The nature of milling means that it is best suited for creating rounded corners. Right angles should be avoided for corners, edges and other part features.
- Avoid deep pockets: Recessed pockets that are too deep can affect the strength of the part, making it susceptible to brittleness or failure.
- Maintain sufficient wall thickness: Similarly, milling should not be used to create thin-walled features, since the material may break under the stress if it is machined too thin.
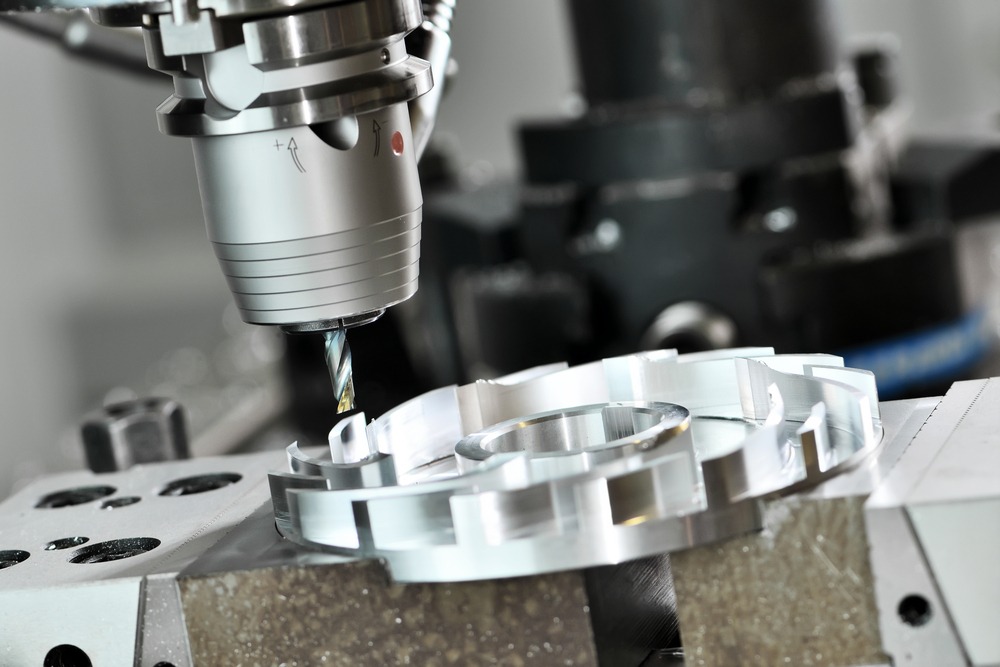
Custom CNC Milling Services from RevPart
With decades of experience in the design and production of plastic products, RevPart is ready to serve you with our CNC milling capabilities. As a leading CNC milling parts manufacturer, we offer the highest-quality materials, exemplary customer service and a focus on success that has led to countless long-term partnerships with our clients. For more information, contact us for a quote.
Why Are CNC Milling Services So Important?
Milling services play a critical role in modern manufacturing because of the precision and efficiency they bring. Whether used for prototyping or creating finished components, CNC milling helps bring products to market much faster than other processes while ensuring high accuracy in meeting specific tolerances.
Frequently Asked Questions
Compared to traditional forms of milling, this process uses precision computer controls, rather than manual control. This means it is fully automated, capable of reproducing consistent results no matter how many times it is performed.
One of the primary benefits of the process is that it does a good job with a wide range of irregular geometries. On top of this, it also makes mass production more efficient after the initial setup is completed.
Yes — parts that have been produced using other methods including die casting or 3D printing can be put through CNC milling to add details and features.
Custom CNC milling produces components with an exceptionally high degree of accuracy to the designs. Typically, these machines can meet tolerances with variations of between 0.01 and 0.03 millimeters.
The average speed of a CNC machine is about one foot per minute. However, there are many factors that influence how long custom CNC services can take. These include the complexity of the design, the kind of materials being machined and the specific tool being used.
At the most basic level, milling means the workpiece is held stationary while the tool rotates around it. On the other hand, turning means the piece being worked on rotates around a stationary tool.
ISO 9001
Quality Control
ISO 14001
Environmental
ISO 13485
Medical
TS 16949
Automotive
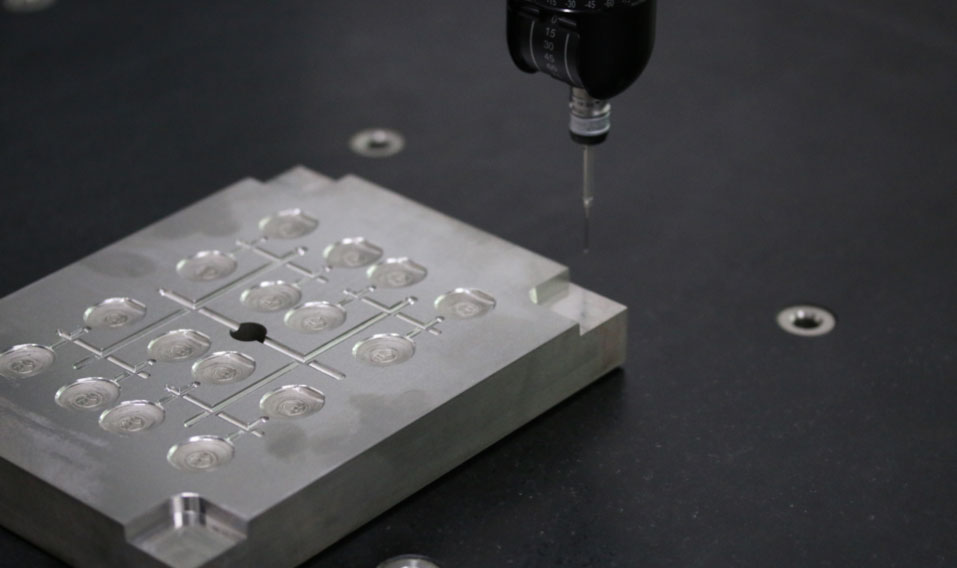
How we succeed
At RevPart, customers are our focus. We believe that by putting the customer first and providing excellent customer service the project in turn will be successful. Click here to learn more about what you can expect when working with us.