The medical industry is a field that sees continuous, ongoing innovation on both a large and small scale. For all the lifesaving and life-improving advances that we’ve seen in our lifetimes (and have read about from even earlier), the scope and velocity of the breakthroughs that continue to advance the industry assure us that the best is likely yet to come.
One large-scale advance that has driven countless smaller scale innovations is the rise to prominence of liquid silicone molding in medical devices and components. The inherent medically friendly qualities of liquid silicone rubber (LSR), combined with continued improvements in its structure and formulation (all of which we will discuss later in this post), have made silicone molding using this material one of the most advantageous ways to operate a business in the medical device field.
There are several different qualities and applications of liquid silicone rubber, and the silicone molding process itself, that make them ideal for use in the medical industry. The material and the process lend themselves to a number of different products, and as LSR has evolved over time, so has its impact on the medical industry — along with the industry itself. Let’s take a look at what’s played a part in these innovations.
The Versatility of Silicone Molding and LSR Across Different Medical Products
The No. 1 quality for any medical grade device or component is its ability to be sterilized. The human body, for all its strengths, can suffer a severe setback from exposure to any sort of contaminant, no matter how minor — especially when the body is already under stress or compromised, as during, for instance, a surgery. One contaminated part or component within a medical device or machine can be just as dangerous as an entire contaminated instrument.
Fortunately, liquid silicone rubber possesses several properties that make it more conducive to sterilization. For starters, LSR can stand up to higher temperatures than thermoplastics that may otherwise be used in medical devices, making it easier to sterilize. The higher elasticity of LSR means that it is better suited to completely filling every corner of a mold, lowering the chances of uneven surfaces or porosities that may be subject to hidden, difficult- or impossible-to-reach contaminants.
In silicone molding, it’s not just the material that needs to be sterile, either. The molds used to produce pieces need to be sterile as well. One downfall of LSR is that it can be difficult to clean the molds used — at least for production-grade molds. The increasing popularity of prototype-grade yet still high-quality molds means that it can be more cost effective to manufacture LSR medical components and devices using those molds designed for limited use in smaller runs, decreasing or eliminating the need to clean them for repeat use — and thus reducing the manufacturer’s liability.
As stated earlier, receptiveness to sterilization is important for each and every component of a medical device or instrument. The particular qualities of LSR make it well-suited to a number of such components, including:
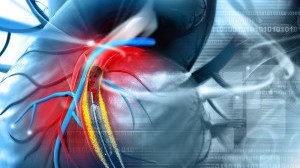
- ● O-rings: important internal components of many medical devices, and can also serve as a necessary contaminant seal for any areas of an instrument that cannot be sterilized.
- ● Nutrition/fluid containers
- ● Tubing: from drug delivery tubes to stomach tubes, LSR is not only easily sterilized but also highly biocompatible, meaning that it will not negatively react with either internal or external parts of the human body.
- ● Internal valves and stents
- ● Catheters
One final point to note for medical components like tubing and catheters— LSR is nearly impervious to discoloration, flaking and other deformities. This quality can’t be underestimated when considering that a medical device that a patient will interact with directly should look safe and sterile, in addition to actually being safe and sterile.
How Have LSR and Silicone Molding Changed the Medical Industry?
Increased innovation in the medical device space often goes hand in hand with increased complexity of parts and components. Assembly, construction and even ideation of such intricate instruments can be prohibitive in many ways, if the difficulty curve is too steep. Silicone molding remedies that, however: the molds created for the injection process can be designed to yield an intricate design in just one piece — little to no assembly required.
Surprisingly, some perceived limitations of silicone injection molding can support the specifics of manufacturing complex medical devices and components. For instance, silicone molding requires much tighter tolerances than molds for thermoplastics — up to 10 times tighter. In other words, LSR will flash at a much smaller margin of error in a mold than a plastic will. However, in medical device manufacturing, precision and tight tolerances are critical — consider the tighter tolerance at which flashing will be produced as a natural failsafe against manufacturing imprecise, often unusable products.
In allowing for greater complexity while requiring greater precision, LSR and silicone molding have played a significant, if indirect, role in driving innovation and change in the medical industry. Other, smaller ways in which the material and the process have affected field are its use in often-overlooked but still critical parts of just about any instrument or device found in an examination room or operating theater.
The handles of surgical tools, for example, are often overmolded with LSR, providing extra grip to support a surgeon’s steady hands. Insulation, from heat to electrical to liquid, is also typically provided by precision silicone components — allowing for more reliable operation of critical, lifesaving instruments. Just about anywhere you look, especially where protecting an instrument, its operator or a patient is critical, you’ll find LSR.
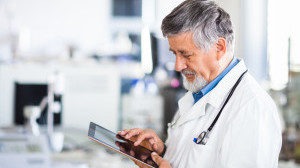
How Has LSR Changed Since its Introduction?
In addition to the more complex constructions allowed by silicone molding, new, more complex formulations of LSR have also played a role in medical innovation. The base LSR synthetic is highly resistant to reacting with skin, membranes and other parts of the human body — internal or external. Over the years, however, biochemists have fine-tuned LSR formulations to allow for even more interaction with the body, to the point where some formulations can be used for devices implanted in the body indefinitely.
Varying LSR durometers, or material hardnesses, have also opened possibilities. More pliable, and thus softer durometers can provide unparalleled grip, as in the aforementioned instrument handles. Increased traction for larger, freestanding devices can also be achieved by creating, for instance, surfaces lined with a soft-durometer LSR. Harder durometers can be used when it’s important to be more impervious to contaminant particles, and easier to clean.
The possibilities of LSR to support innovation in the medical field are broad and far reaching — and still growing and changing, with opportunities to make an impact readily available.