Great product designers are always on the lookout for better ways to reduce cost and improve the user experience. Living hinge design is method that can accomplish both these tasks handily by replacing conventional hinge design methods with a flexible thin web of plastic. Due to the unique flow dynamics of plastic injection molding two bodies of plastic can be connected with a resilient hinge can be cycled indefinitely. What is the key to getting a quality plastic living hinge? It’s all about the design…
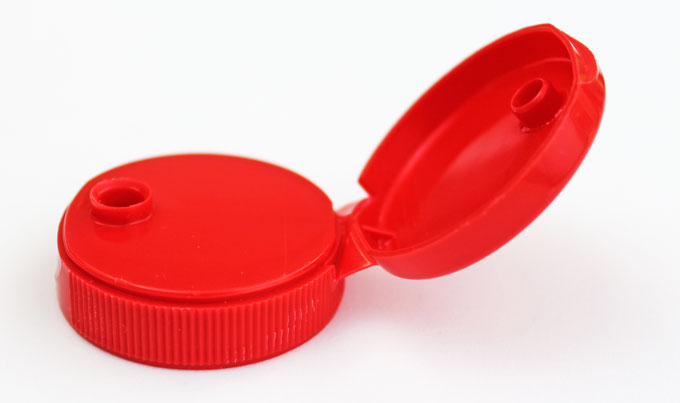
What is a living hinge?
A living hinge is a thin section of plastic that connects two plastic bodies together. Since it is very thin it enables the two bodies to move rotationally to angles of 180 degrees and greater. They are very durable and with good design can last for millions of cycles. A familiar example would be a ketchup cap. The purpose of the hinge on a ketchup cap is to keep the cap connected to the main body but also allowing it to move out of the way for dispensing.
What are living hinges used for?
When you need something that connects two sides together and allow rotational movement a living hinge will likely do the trick. It can take the place of a traditional hinge in most cases and do it with less parts and no assembly.
You will find living hinges on plastic parts like caps and closures. Common examples include:
- • Makeup compacts
- • Candy container caps (for example Tic Tac mints)
- • Look in your fridge sauces, condiments and more have living hinges
- • Shampoo and liquid soap bottles
- • Fishing tackle and lure boxes
What benefits will I get by using a living hinge over other types of hinges?

Eliminate assembly and lower cost – Plain and simple this is the biggest advantage of a living hinge. Most conventional hinges require some type of pin like a screw or metal rod be inserted for the hinge to turn. Since a living hinge is a uni-body design you can eliminate those parts off the bill of material. Not only do you eliminate the hardware but you get rid of the hassle and cost of assembling the hinge.
Eliminate the need for multiple cavities – Without the living hinge the two halves would be separate parts which would require separate cavities, gates and runners. Since a living hinge connects both half the cavity becomes one and will typically reduce the cost to make the mold.
Durability – A properly designed and applied living hinge can last well over a million cycles. Most cycle test usually give up around the million cycle mark so it is conceivable that they can last many more cycles.
Reasons not to use living hinges?
Limited material selection – The best material for a living hinge is Polypropylene PP. Polyethylene PE can be used in some situations. Even when using PP and PE you are limited on the types of additives and fillers you can use. If you need to use an engineering grade plastic such as polycarbonate or ABS then a traditional hinge would be a better fit.
Limited load bearing – Living hinges are not very good at bearing a load parallel to the hinge. A good example would be a door. A door has significant weight and places a load on the hinges it is attached to. The hinges must bear the load of the door and swing open and closed. A living hinge is not good for an application that places this kind of load on them.
Added development time – Living hinges require some time and effort to design. Each application is different and presents a unique set of challenges. In my experience after the injection mold is made the living hinge feature often requires some type of adjustment to get it working perfectly.
Living hinge design considerations
When it’s time to design your living hinge it is very important to follow some basic design guidelines to ensure the hinge will function as intended.
Typical living hinge designs
• Flat hinge – the strait hinge is the most common type of living hinge. It consist of a landing in both sides and a thin hinge section.
• Double Hinge – A double hinge has two strait hinges separated by a narrow landing section. Double hinges are useful when you need to A) Create a gap or space between the two folded parts or B) You need a 360 degree rotation.
• Butterfly hinge – A butterfly hinge is commonly used on dispensing caps. The big advantage of a butterfly hinge is its flipping action. Once the hinge is opened/closed past a certain angle the hinge will spring to the other position and stay there. So the cap will flip to the open or closed position.
• Bi-stable Hinge – this is very similar to the butterfly hinge only instead of one uniform living hinge there are three separate hinge sections. This design will result in strong opening and closing action. The hinge is in equilibrium in the open and close position thus the name bistable hinge
Living Hinge Design Guidelines for Injection Molding
Living hinge design is no doubt an art as well as a science that comes with experience. It is common to make a few changes to the mold after testing the first parts and with small tweaks the design is normally honed in to a functional hinge. While there are many different types living hinges and probably some yet to be discovered we will go over the basics of what makes a living hinge work.
Web Thickness
the thickness should range between 0.007” – 0.015” thick. Anything thinner than this and the plastic may not fill the hinge section properly in the mold. Anything thicker and the molecules will not orient in the right direction which will effect cycle durability.
No Sharp Corners
It’s a good idea to radius sharp corners when designing for injection molding. It’s even more imperative to radius sharp corners in and around the living hinge. The increased stress in sharp corners will reduce durability.
Gate placement
Ask RevPart for your gate location and we can give you a CAD drawing of your mold. You want to make sure that the flow of plastic will evenly distribute along the hinge. This typically will require a gate that is centered on the hinge.
Hinge Material
Selecting the right material is critical to good hinge design. A good resin choice should flow well though thin areas and should not stress crack when flexed. Only two types of plastic are acceptable:
Polypropylene PP is the best resin choice for living hinges. When reviewing your PP material options look for a Homopolymer PP. This type of PP constantly performs well and produces durable living hinges. Random Copolymer PP is the second best choice and will perform very well. Impact Copolymer is the least desirable for hinges and should only be used if you have a low temperature or impact strength requirement.
Polyethylene PE the second choice but PE but is seldom used. PE should only be used is PP isn’t an option.
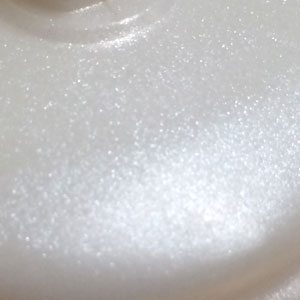
Fillers and hinge life impact
Adding fillers is a common way to achieve certain requirements for the resin. For example you could add glass fiber to increase tensile strength or add Perl flakes for a metallic appearance. Additives like Glass, talc and fiber may negatively impact the durability and functionality of your hinge design. It is not suggested to use any fillers and if it is determined to be necessary then it is suggested to R&D the hinge with a prototype mold.
Mold Flow a living hinge at the molecular level
The key to getting a durable living hinge is getting all the plastic molecules to align instead of being randomly oriented. When molten plastic flows though the mold cavity it is forced through the small area of the hinge. The flow direction of the plastic and increased speed will create a molecular alignment along the hinge. The molecules with be oriented perpendicular to the flex direction which will extend the durability of the hinge.
Another important consideration in hinge design is having uniform flow along the hinge. Flow that is not uniform increases the chance of having weld lines or defects which could compromise durability. No need to worry at RevPart we do a flow analysis and choose the best gate entry point for your mold. This ensures you will get uniform flow along the hinge and get durable parts as a result.
Environmental factors to consider
UV exposure – Polypropylene like most plastics will degrade with UV/sunlight exposure. If you have UV exposure requirements it is highly recommended to add UV additives or a UV protective coating. Prolonged UV exposure tends to create fractures in plastic which will affect the longevity of a living hinge.
Chemical exposure – If the part is going to be exposed to chemical then it is important to make sure that the selected resin will not be degraded.
Post processing
A common post process named cold drawing is to flex the hinge while it is still hot. The hinge is usually flexed a few times as soon as it comes out of the mold. By flexing the part while it is still hot further orients the molecules in a direction that increases durability. One caveat is that it is very time consuming to do this and it will increase manufacturing cost. If your cycle requirements are less stringent then you can often skip this post process and the cost associated with it.
Prototyping living hinges
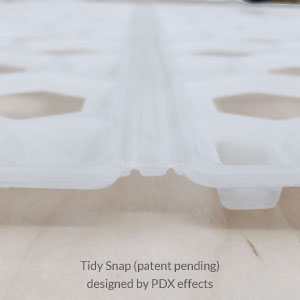
Prototyping is a valuable tool that allow you to revise your part without a large investment Using Traditional methods, prototyping a living hinge is not possible due to its strict dimension and material requirements. However due to RevPart’s proprietary CNC machining processes we are able to CNC machine many types of living hinge designs out of Polypropylene. Hinges come out fully functional and have the ability to be cycled hundreds of times. Another option is to open a prototype injection mold to R&D your living hinge design.
Check out the SlideShare
Final tip
Design your living hinge for tool-safe changes. This means you’ll design your hinge slightly thinner than you actually need. This way, you can make tooling changes without much impact to the mold itself.